Become an Expert in Purchase Price Variation and Costing Methods……
What is Purchase Price Variation or PPV?
Purchase Price Variance (PPV) is the difference between the Unit Price paid for a specific item within a purchase order line item and the “Standard Cost” of that item. An Item “Standard Cost” is typically defined within any Business Software as the “typical” unit price expected to be paid for the item. During each Purchase Order receipt process, a PPV is recorded for each line item received. It is common practice for Business Software to update its Items’ “Standard Costs” regularly using the PPVs recorded over a specific time frame.
Costing Methods Explained
Standard Costing
Most ERP software has a field in its item master that identifies a “Standard cost.” As stated previously, this is the typical unit price or cost used to determine the cost of the material. Standard costs can be updated regularly, typically by looking at the historical purchase history of unit prices and quantities to update the Standard Cost.
Last Costing
Most ERP software has a field in its item master that identifies a “Last Cost.” This is the last unit price or cost of the material. The Last Cost fields within an item master typically update after the first purchase order receipt of an inventory item.
Average Costing
Most ERP software has a field in its item master that identifies an “Average Cost.” This is the average unit price or cost of the material over time. Average costs can be updated regularly, typically by looking at the historical purchase history of unit prices and quantities over a period to update the Average Cost.
Actual Costing
Some ERP Software utilizes a First-In, First-Out (FIFO) inventory process by recording an entry into inventory for each purchase order receipt. Each Purchase Order receipt captures the item, the received date, unit cost, and quantity received. When used, the material consumed within a work order is selected from the FIFO inventory. This process allows manufacturers to understand the actual cost of the material used to complete each work order.
Cost Variation View
Some ERP Software, like SimpleManufacturing™, displays Standard, Last, and Average Costs within the Item Master. Click here to view more information about the Item Master module within SimpleManufacturing™. In addition, most indicate the last time the information was updated. As shown below, the variation between Standard, Last, and Average Costs can be significant and dependent on the variation of purchase quantities, unit cost, and Vendor.
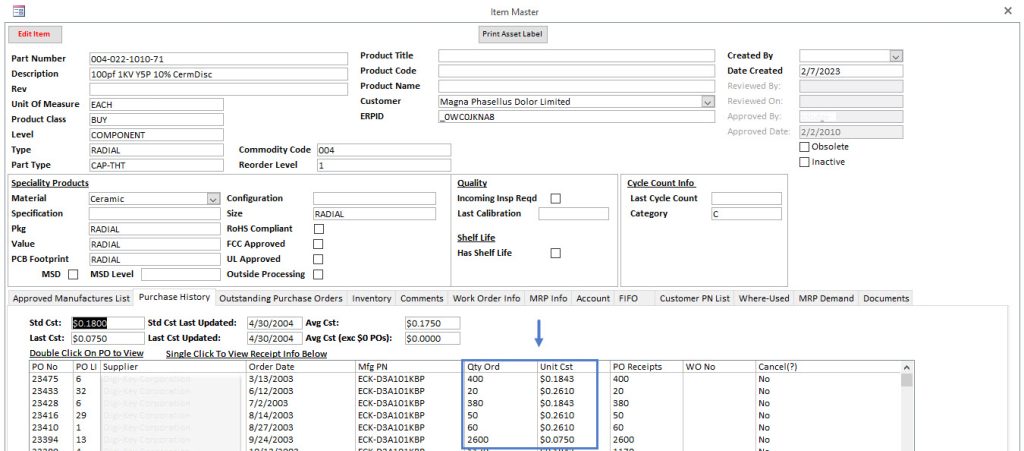
Why Do So Many Companies Use the Standard Costing Method?
Below is a list of reasons Many Companies use the Standard Costing Method.
- Some would argue that the Standard Costing method simplifies the accounting side. The standard cost is charged for every material item received into inventory, every item completed in manufacturing, and each product sold can be added consistently regardless of the actual unit prices paid. Some ERP Software, like SimpleManufacturing™, uses actual costing without any additional requirements for its users, including accounting personnel. Click here to view more information about SimpleManufacturing.
- Buyers and Purchasing agents can view the standard cost of an item as what they should reasonably pay, per unit, of the item. Provides a benchmark.
- Alert management only with Large Purchase Price Variances, leaving more time for managers to focus on other issues.
What are the Disadvantages of Using the Standard Costing Method?
- Standard Cost does not accurately represent the actual cost of material added to the inventory of each unit completed through manufacturing or sold. Identifying the Actual costs of each unit shipped accurately identifies if the business made a profit on each unit shipped.
- Standard Cost is old information and was only accurate when it was last updated. Reviewing variances that are a month old or from a past period is almost useless. Budgeting and basing decisions on old information requires more scrutiny. Otherwise, it may result in adverse results.
- Buyers and Purchasing agents can view the standard cost of an item. Still, they must also be provided with historical purchase information to see the actual unit costs, purchase quantities, and dates to make a more informed decision about expected unit prices. SimpleManufacturing™ provides users with quick access to historical purchase order information to make informed decisions on how much they should expect to pay for material given the quantity they need to purchase. Click here to view the SimpleManufacturing™ Item Master module, features, and functions.
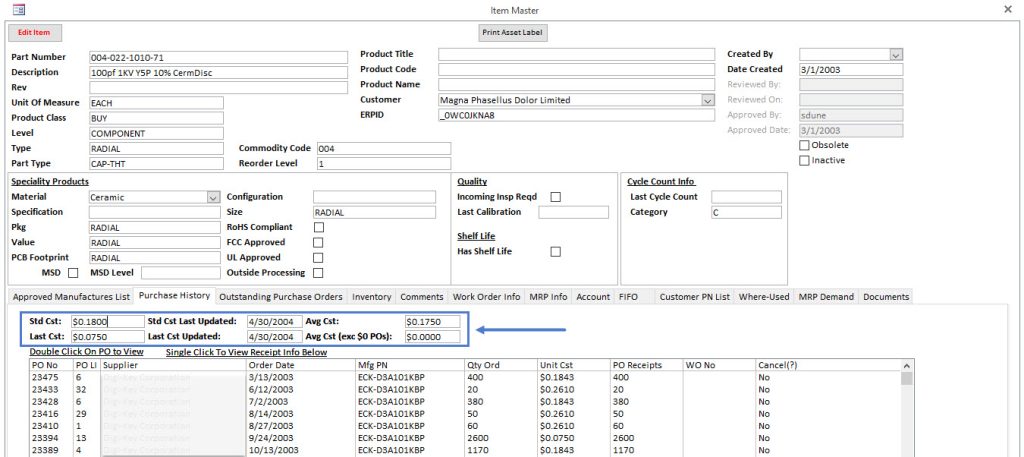
- In reality, management reviewing significant variances of Standard Costs is rare. Most have found that several variables cause legitimate significant variances they cannot control. Variables include significantly different purchase quantities, using multiple vendors due to stock availability, and the lack of regularly updating Standard Costs.
Why SimpleManufacturing™ uses Actual Costing?
- SIMPLICITY!
The actual costing method represents a simple costing method. With actual costing, businesses know the actual costs of materials and outside processing services—no need for complicated formulas, spreadsheets, or sophisticated equations that factor in variances. Actual Costing yields an accurate profitability amount for the material and outside processing portions of a unit cost.
- ACCURACY!
Standard Cost is used for budgeting purposes only. Actual Costing uses the actual costs incurred during the specified period. This method offers more accuracy because the business isn’t estimating what it costs to perform the manufacturing process. While the other methods, such as Standard Costing, may offer more stable results, Actual Costing accounts for the variable costs that arise throughout the manufacturing process. This variation helps businesses understand their inventory and consumption cost variances more comprehensively.
The Difference in Costing Methods shows very different results in Profitability.
Below are the different costing methods and the Profitability of Units Shipped. The results are astounding. Choosing the proper Costing Method for your ERP Software may determine your business success and sustainability.
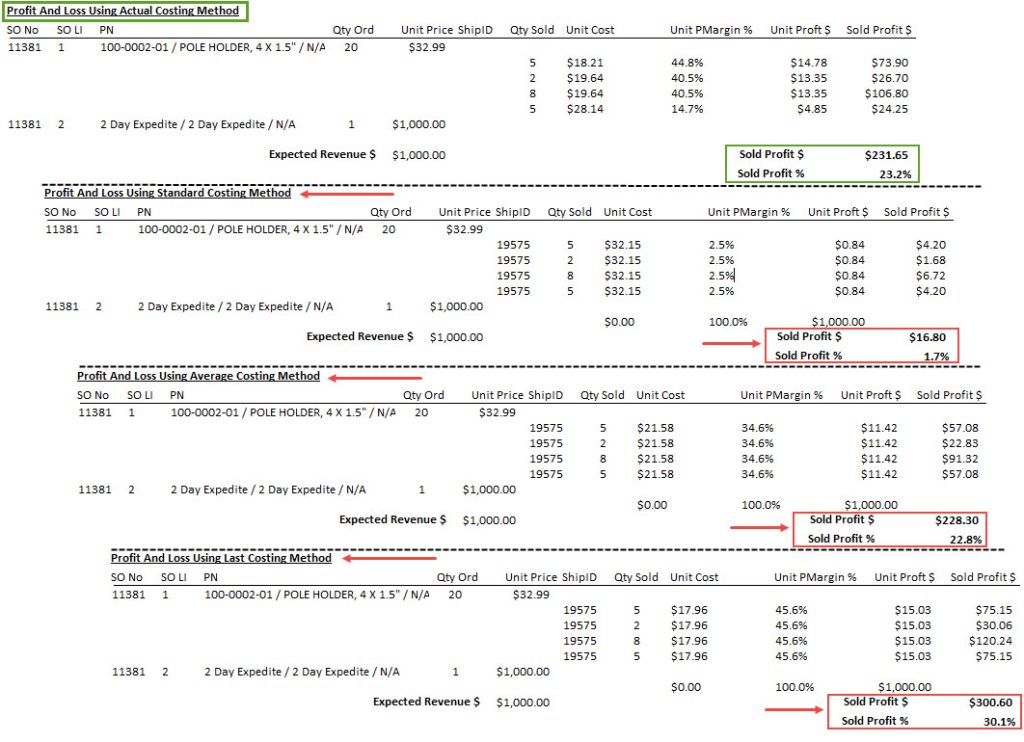
Choosing SimpleManufacturing™ as your next ERP / MRP Manufacturing Software Solution
The ERP Software you choose now will determine your company’s success. Please pay particular attention to its scalability, current features, and ability to be modified to meet your future business needs. Our flexible approach, focusing on efficiency and seamless integration with your current processes, with the expectation of change, provides a long-lasting solution.
Nice share!